
In the logistics and warehousing industry, the labor landscape is evolving rapidly. A staggering 73% of warehouse operators struggle to source enough labor to meet the demands of business.1 The significant labor shortage is compounded by shifting demands, peak season surges and the growing complexity of supply chain operations. Navigating these challenges requires strategic labor planning to ensure operational efficiency and resilience.
Why labor planning is business critical
Labor planning is critical in warehouse management as it encompasses the labor forecasting, scheduling and allocation of workforce resources to meet operational demands. Effective labor planning ensures the right people are in the right places at the right times, which directly impacts productivity, cost efficiency and overall operational success. Inadequate labor planning, on the other hand, can lead to bottlenecks, increased operational costs and failure to meet customer expectations—ultimately affecting the bottom line. Moreover, strategic labor planning enhances employee satisfaction and retention by preventing burnout and optimizing work conditions, which contributes to a more stable and efficient workforce.
Key factors of labor planning
Labor planning involves certain strategies to get it right:
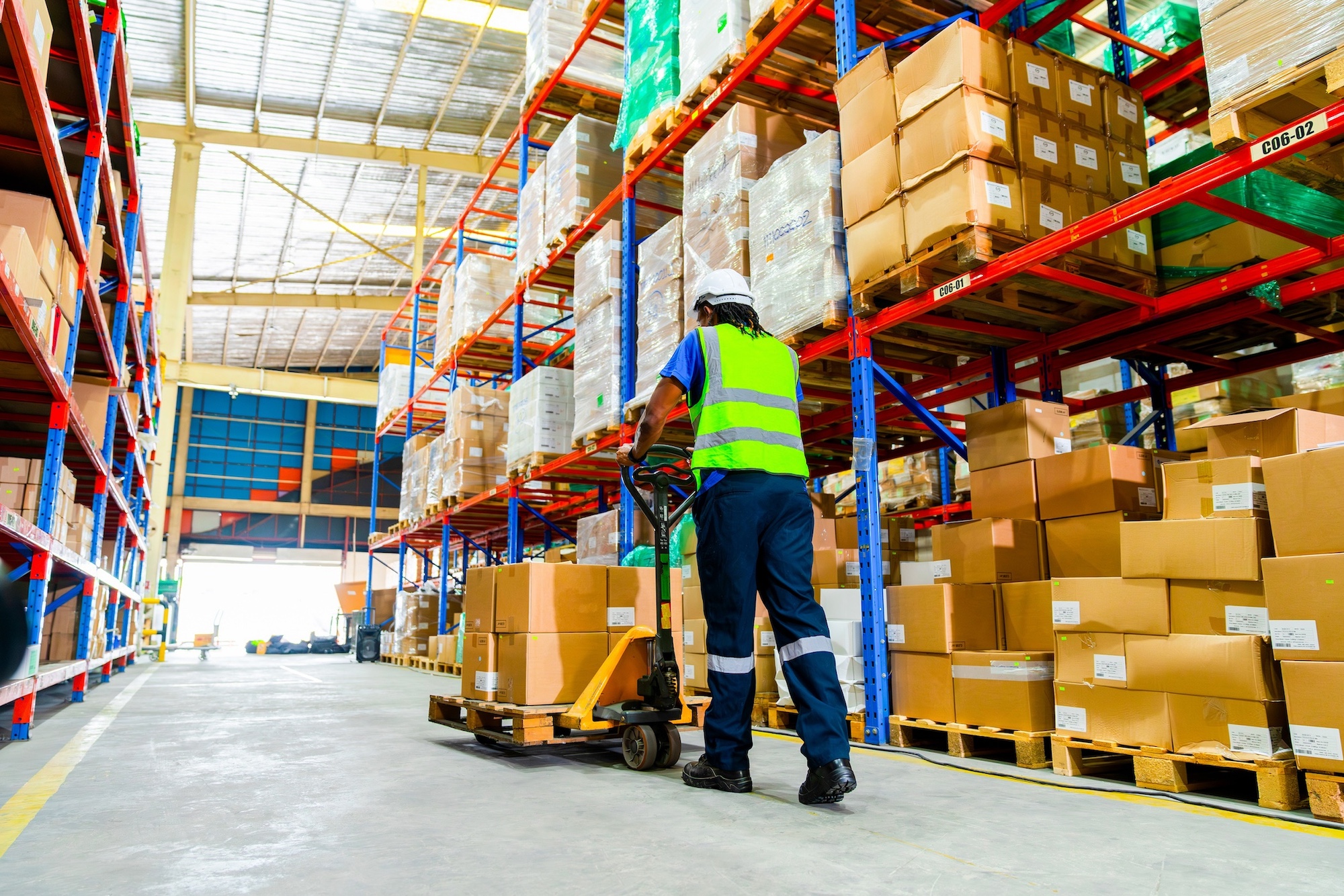
- Labor forecasting: Predict future labor needs based on historical data and anticipated demand. Accurate forecasting allows for proactive adjustments to staffing levels, ensuring readiness for both peak periods and slower times.
- Skill analysis: Identify the competencies required for various roles in the warehouse. Analysis involves determining the specific skills and certifications needed, enabling targeted hiring and training programs to fill gaps and enhance overall productivity.
- Seasonal adaptability: Adjust labor plans to account for peak seasons and fluctuating demand. Effective management of seasonal variations helps maintain optimal workforce levels, preventing both overstaffing and understaffing during different periods.
- Labor cost tracking: Evaluate labor costs alongside relevant metrics for your business. For example, labor cost per unit shipped or labor-to-revenue ratios are data points that enable warehouse operators to assess the efficiency of their operations, ensuring that labor expenses are aligned with revenue and operational goals.
Challenges in labor planning
When it comes to warehouse labor planning, the complications warehouse operations face include:
Fluctuating demand: Warehouse operations are often subject to fluctuating demand and seasonality, which can make labor planning challenging. Peak seasons, promotional periods and unexpected surges in order volumes require dynamic labor management strategies to avoid understaffing or overstaffing.
Labor shortages and skill gaps: According to the Council of Supply Chain Management Professionals (CSCMP), 73% of logistics companies report experiencing labor shortages, with 58% stating that it impacts operations significantly.2 Additionally, the varying supply of skilled workers complicates labor planning. Identifying and retaining employees with the necessary certifications and specializations is crucial to maintain operational efficiency.
Strategies for workforce optimization
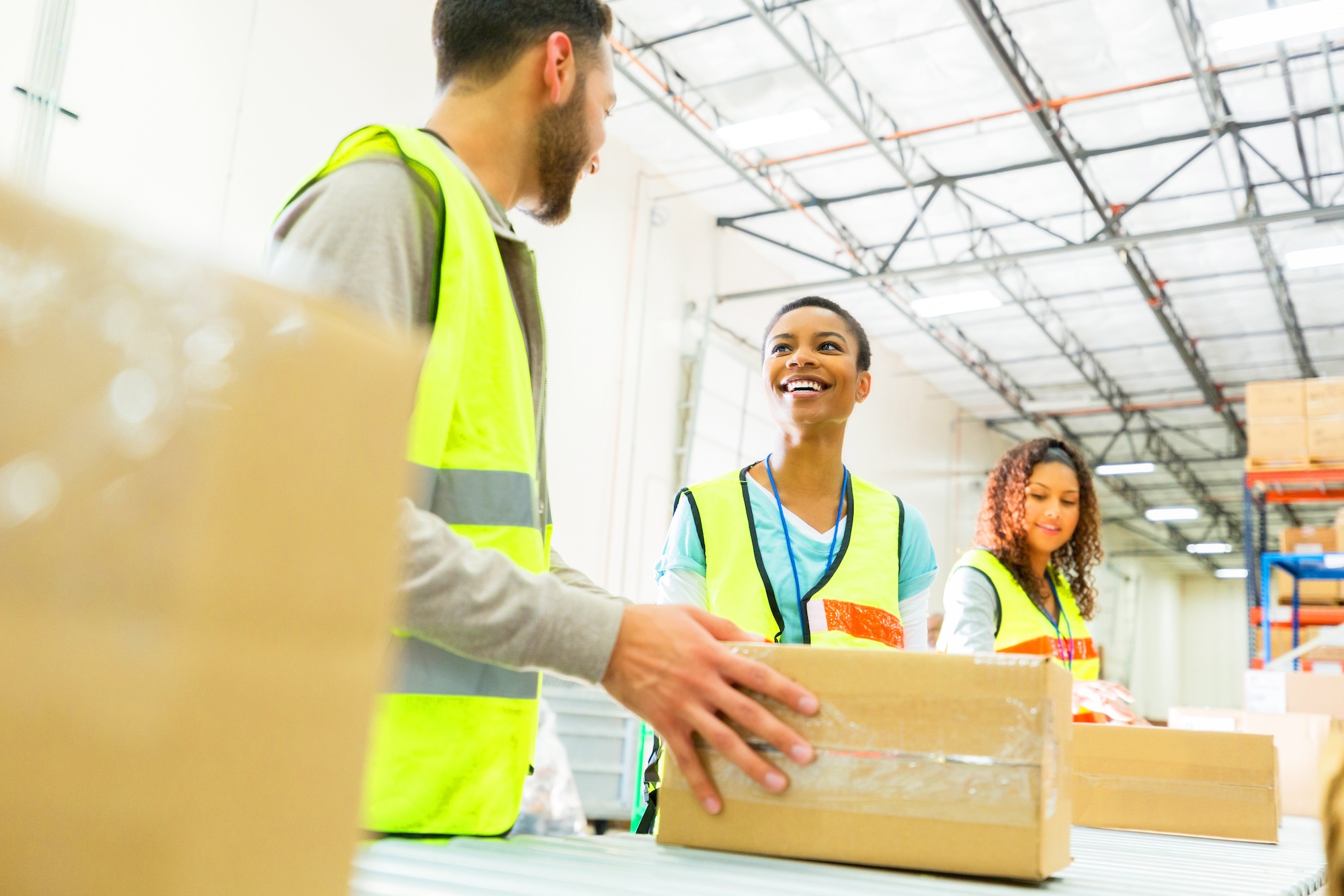
Assess current and future staffing needs: Understanding your staffing needs involves a thorough assessment of current workforce capabilities and future requirements, which can be achieved through:
- Demand forecasting: Use historical order data and predictive analytics to anticipate the ebbs and flows of your business.
- Skill analysis: Evaluate the skills required for different roles and identify gaps in your current workforce.
- Workflow analysis: Analyze how goods move through your facility to identify areas where labor can be optimized.
Access flexible warehouse staffing solutions: Flexible warehouse staffing solutions— such as part-time, temporary and seasonal workers—can help address fluctuating labor needs. Platforms that provide on-demand access to a pool of vetted workers can be invaluable during peak periods.
Cross-train employees: Cross-training your workforce to perform multiple roles can create a more adaptable workforce, which helps cover absences, enhance job satisfaction and reduce turnover. An adaptable workforce can shift between tasks, improving operational resilience when shorthanded.
Integrate technology and automation: Augmenting a workforce with technology can enhance productivity significantly and mitigate labor shortages. Automation can also enhance labor productivity. Some effective technologies include:
- Autonomous mobile robots (AMRs): AMRs navigate warehouses independently to transport goods, reducing the need for manual labor in repetitive tasks, such as picking, sorting and moving inventory.
- Labor Management Systems (LMS) and Warehouse Management System (WMS) Integration: Integrating LMS with WMS allows for real-time tracking of inventory and labor, streamlining workflows and reducing errors. This cohesive management approach enhances workforce utilization, enabling faster order fulfillment and more efficient, cost-effective warehouse operations.
Prepare for the future of your warehouse labor needs
As the industry continues to face a surge in demand that coincides with labor shortages, strategic labor planning can ensure efficiency and resilience. By assessing current and future staffing needs, implementing flexible warehouse staffing solutions, cross-training employees, and integrating technology and automation, warehouse operators can navigate labor challenges, maintain operations, reduce costs and meet the evolving demands of the logistics industry.